Faculty project recognized as breakthrough by National Science Foundation
Breakthrough technology by a team of researchers at The University of Akron (UA) has the potential to benefit motorists and positively impact the safety of tires.
Dr. Siamak Farhad, associate professor of mechanical engineering, and his team developed a new system they refer to as high-frequency dynamic mechanical analysis (DMA) that, for the first time, directly and accurately tests new materials that go into making tires. The system was recently featured by the National Science Foundation (NSF) as an Industry-University Cooperative Research Centers Program (I/UCRC) breakthrough story as it can lead to significant process improvements or techniques.
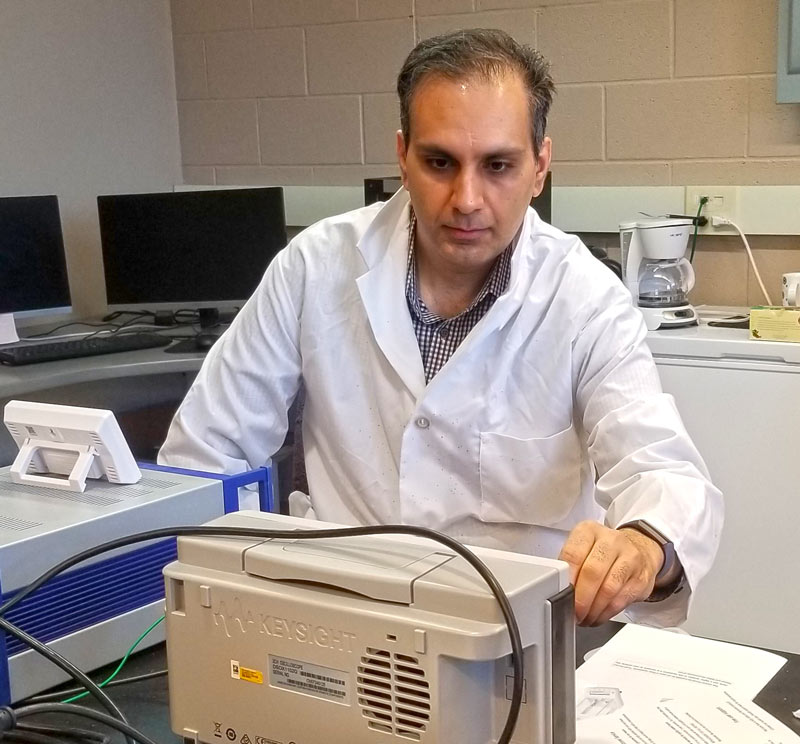
Dr. Siamak Farhad inspects his team’s high-frequency dynamic mechanical analysis system.
Farhad answered some questions about his team’s latest breakthrough, which was supported and guided by the Center for Tire Research (CenTiRe). CenTiRe is a consortium of UA, Virginia Tech and several industry company members that conducts research in the materials and physics of tires.
What is a dynamic mechanical analysis?
“DMA is a test system that can be used to study the mechanical behavior of a type of materials which are both elastic like a spring, and viscous like honey. One of the best examples of such a material is rubber. Most DMAs work by applying a force at different speeds to the material and then measuring the material’s deformation. The DMA is available on the market; however, the current system cannot apply forces at high speeds.”
How does this new system work? What problem does it solve?
“This new test system works based on applying a force at a specific speed repeatedly to the material and the material deformation is measured. This new test system can apply forces at higher speeds than the test systems available in market. Thus, the materials for applications such as tires, automobile paints and shock absorbers can be characterized directly in a broader range of operation. The outcome will lead to better materials for improved productions.”
What influenced you to develop this new system?
“The need of industry. In fact, the lack of direct and accurate test system to study the behavior of some materials and realizing this need from tire industry members of CenTiRe were the main reasons that this new system was developed. I would like to take this opportunity to thank CenTiRe for providing the opportunity to collaborate with industry. We actively partnered with 20 companies, some of them international, through CenTiRe.”
How is this system different from what is already available in the tire industry?
“The test systems currently available on the market cannot do the test directly when the force should be applied at high speeds. To address this issue, the available DMAs use some mathematical equations to manipulate the test results to estimate the behavior of materials, but this estimation is not very accurate.”
What are the potential applications? Who will be able to use this?
“This new test system can be used to study the behavior of some materials, where they are used for applications that materials experience forces at high speeds. This test system can be potentially used in rubber industries, coating industries and in the U.S. Army.”
What’s next in this development process and research?
“The next step is to add a temperature control chamber for testing materials at different operation temperatures.”
When do you hope to have a product commercially available?
“If the commercialization funds are available, I hope that the first commercial prototype will be ready in 2021.”
Your research and system were featured by the National Science Foundation as a “breakthrough story.” As a researcher, how does that make you feel?
“I am happy that this project has been featured 'breakthrough story' by the NSF. This motivates me significantly to explore the industry needs and research gaps in my field and try to address it. It is necessary to acknowledge the role of Dr. Roja Esmaeeli, who was a graduate student working on this project, and several UA undergraduate students who helped and made the project successful.”
How did you come to choose your career?
“I had experience in working in both industry and academia. My first full-time industry job was in a company that I was working with a team to establish vehicle safety test procedures. At that time, I was also collaborating with a university research center, almost every evening and sometimes on weekends. This collaboration was continued during my six years working in the vehicles and energy industries until I finally decided to join academia because I enjoy both research and teaching. Currently, most of my research activities are with industry.”
What does the next 10 years hold for your field?
“I think online teaching tools and incorporating artificial intelligence into my research will be helpful to improve the quality of my research and teaching activities.”
RELATED
Media contact: Alex Knisely, 330-972-6477 or aknisely@uakron.edu.